Trending Blogs
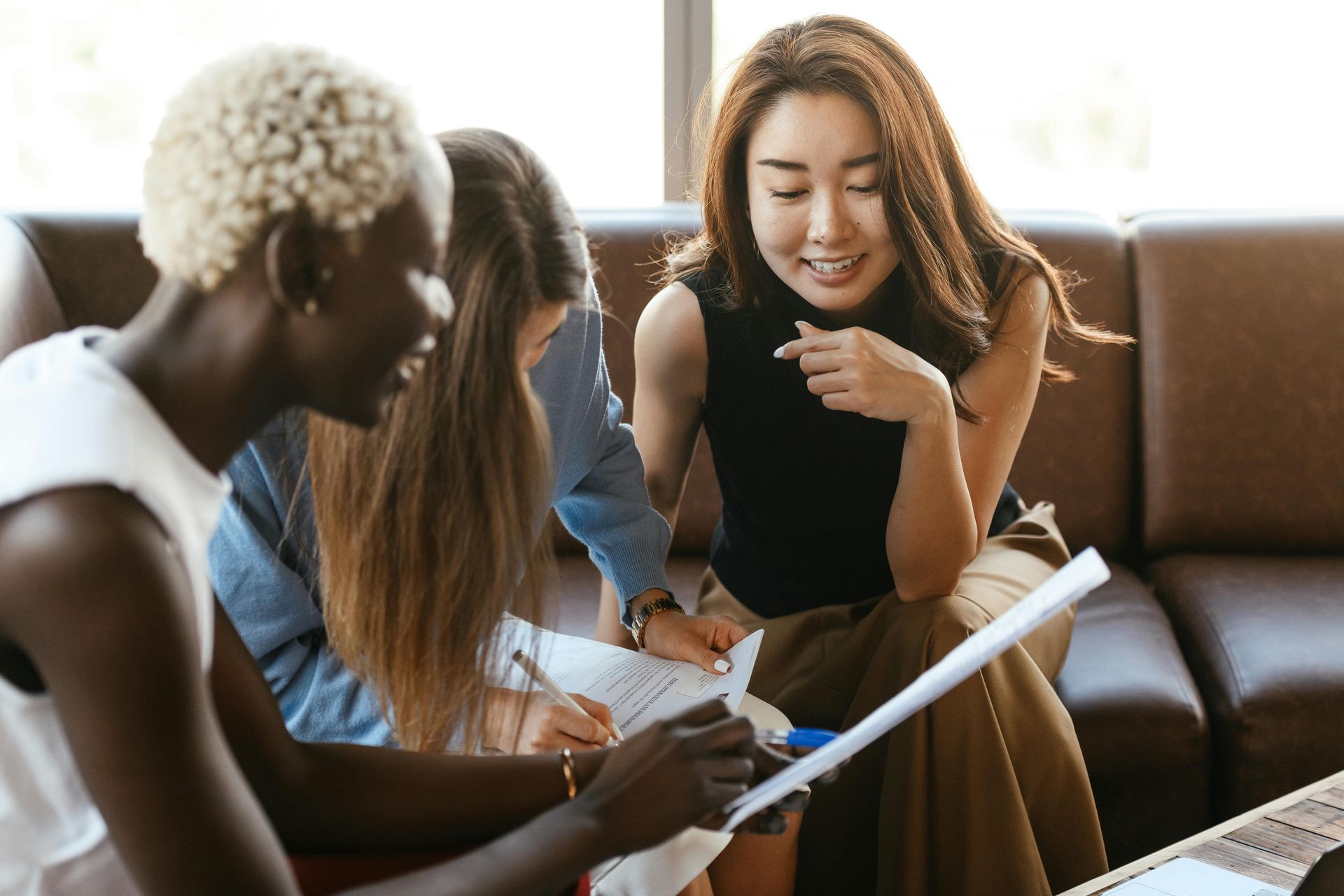
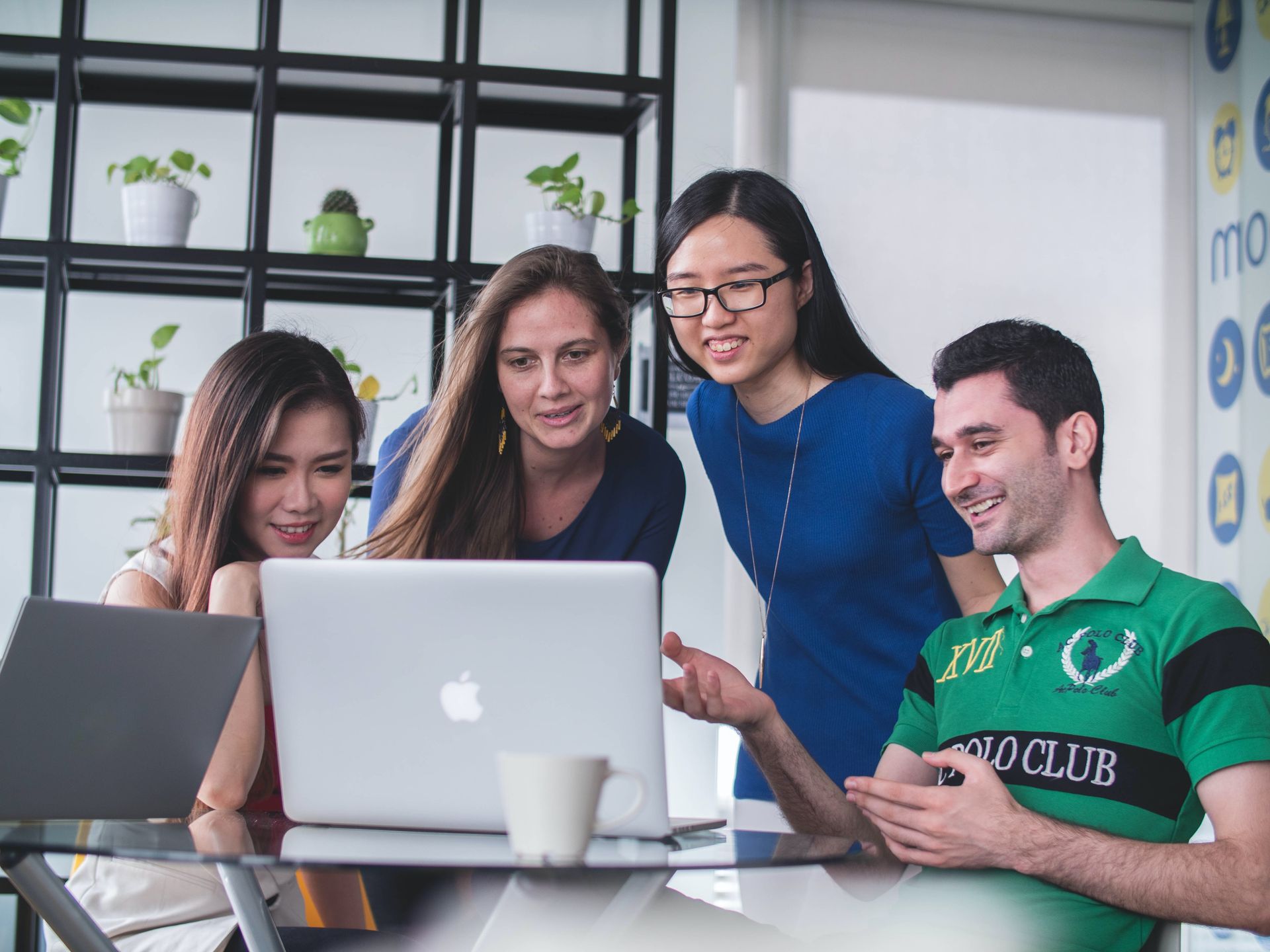
IN THE SPOTLIGHT: INTERVIEW WITH A LEAN/SIX SIGMA PROGRAM MANAGER
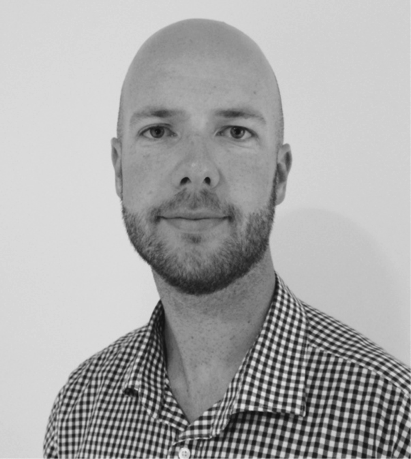
PETER GAFFNEY
TRANSFORMATION PROGRAM MANAGER
METRO TRAINS
As a contractor who specialised in Lean/Six Sigma Program Management, where do you see your role fitting within an organisation embarking on a major transformation?
The role is critical from both a consultative and delivery aspect. It is important that at the outset you are aware of and understand what you were engaged to achieve and the motivation behind this. From this point you then begin to add value to the engagement by creating a road map/strategy to the original request i.e. ‘Option 1’; and more often than not, a road to map to an ‘Option 2’ which is usually what the business actually wants to achieve and only becomes visible through your experienced input.
It is common that a delivery stalls or does not meet expectations, this is more often than not attributable to not correctly identifying the customers genuine requirements or a delivery road map that is lacking thorough development. Thus, the role is that of a guide with the necessary tools and experience to develop an appropriate, realistic and effective strategy that you would be personally prepared to deliver.
What do you think are the key qualities a Process Improvement/Lean/Six Sigma specialist should possess?
There are many, but the foundational are:
- Recognition that Lean/Six Sigma are good tools, but are only tools among many in a good repertoire.
- Insightful; both from a business process and stakeholder management aspect.
- Strategic vision; the ability to see the big picture and then align the deliverable(s) with this.
- Flexible; goal posts are often moved for a myriad of reasons, be prepared and able to move with them.
- Hard working; the nature of this work is such that there will be periods of above average demand on your time.
- Hungry; you must be someone who seeks continuous improvement.
- Analytical; in all ways i.e. numerically, people, process ect.
How does an organisation best tackle Lean/Sig Sigma transformations?
Engage with specialists. Internal development of such capability is a better long term strategy but does take significant time. If you have a transformation requirement that is on the horizon or immediate then you need to engage external professionals to ensure it is scoped properly and will actually get delivered.
What advice would you give to an organisation embarking on a Lean/Six Sigma project for the first time?
Ensure you are clear on what you want to achieve and understand how it aligns with your organisation's strategic direction. Good professionals will then assist with quickly firming this up. If you engage or begin without having put thought into this you will find yourself dissatisfied early in the piece with a perceived lack of progress, which can do a lot of damage to key stakeholder’s perception both at the time and moving forward, thus almost immediately putting you on the back foot.
What has been your biggest achievement resulting from a Lean/Sig Sigma project to date?
The rapid progression of my career and value of my opinion by senior members of my current organisation. To work in this field and be known as someone who ‘delivers’ is my single greatest achievement.
What are the benefits to working on an interim basis versus taking on a permanent role with an organisation?
The benefit of working on an interim basis is that although you will undoubtedly have more expected of you in a much shorter time frame, you are then a in a position to learn, grow and deliver more in much shorter time frames; a win-win for both your employer and yourself.
For more information on Process Improvement roles or for further market information, please contact Laura Frazer at Project Resource Partners on 9949 8103 or
lfrazer@projectresourcepartners.com